Un défaut de moulage est une irrégularité indésirable dans une pièce de métal obtenue par moulage, et caractéristique du procédé d’obtention. Certains défauts peuvent être réparés mais ils peuvent aussi mener au rebut de la pièce.
Types de défauts
On peut distinguer cinq catégories de défauts, en se fondant sur leur mécanisme de formation : les défauts formés pendant le retrait lié à la solidification, ceux dus au gaz, ceux liés au matériau avec lequel est réalisé le moule, ceux formés pendant le remplissage du moule et les défauts métallurgiques. L’apparition d’un défaut peut toutefois résulter de la combinaison de plusieurs phénomènes. Un correctif apporté au procédé pour éviter la formation d’un défaut peut aussi créer un défaut d’un autre type.
Défauts dus au retrait de solidification
Les défauts de retrait apparaissent lorsque le métal liquide ne parvient plus à compenser les contractions dues à la solidification du métal. On peut distinguer les défauts débouchant sur la surface de la pièce de ceux restant à l’intérieur de la matière. Les défauts visibles de la surface sont les « criques débouchantes », qui s’apparentent à une déchirure de la peau de la pièce, et les « dépressions » qui sont une déformation concave.
Les défauts dus au retrait restant à l’intérieur de la pièce, appelés « retassures », sont des cavités que le métal liquide n’a pas pu remplir pendant la solidification. Ce sont des zones où une poche de liquide est restée isolée : la cavité se situe généralement au sommet de la poche de liquide. Pour qu’une poche de métal liquide se trouve isolée, il faut donc que le procédé de remplissage du moule soit incompatible avec les formes de la pièce. La présence d’autres défauts (impuretés, bulles de gaz,…) peut aussi perturber la solidification et piéger le métal liquide
On lutte contre la formation de ces défauts par un dimensionnement et un positionnement correct de masselottes, qui vont alimenter la pièce en métal liquide au cours du retrait. Si elle est correctement conçue, la masselotte est alors la dernière zone solidifiée et il est normal qu’elle soit constellée de défauts dus au retrait.
Défauts dus au gaz
Porosités sur un cube de lutécium de 1 cm de coté.
Les « porosités », ou les « soufflures » si le défaut est plus important et ponctuel, correspondent à la formations de bulles de gaz dans le métal pendant sa solidification. Ce phénomène est dû au fait que la plupart des matériaux peuvent contenir une plus grande quantité de gaz dissous à l’état liquide qu’à l’état solide. Le gaz dissous est donc rejeté au moment de la solidification, jusqu’à former des bulles. Ces bulles sont facilement décelables lorsqu’elles débouchent à la surface de la pièce : elles apparaissent comme une « piqure » ou un cratère. Elles peuvent également rester piégées au sein du métal, affaiblissant alors dangereusement la pièce moulée. L’azote, l’oxygène et l’hydrogène sont les gaz les plus fréquemment trouvés dans les soufflures. Dans l’aluminium en fusion, l’hydrogène est le seul gaz susceptible de se dissoudre dans des quantités suffisantes pour créer des bulles de gaz : pour des pièces de quelques kilos, le dégagement d’hydrogène génère une porosité avec des cavités mesurant de 0,01 à 0,5 mm, qui dépassent même 1 mm de diamètre sur les grosses pièces moulées.
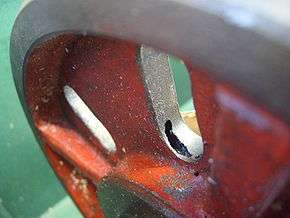
Pour limiter l’absorption de gaz par le métal en fusion, on peut traiter le métal avant la coulée, en le maintenant sous une couche de laitier, sous vide ou sous une atmosphère de gaz peu solubles, comme l’argon. On limite aussi la solubilité des gaz en travaillant avec des surchauffes (écart entre la température de coulée et celle du liquidus) faibles. Réduire les turbulences au moment de la versée du métal dans le moule, en travaillant la forme des canaux d’alimentation et la vitesse de remplissage est également favorable. Sécher le moule évite aussi les reprises en hydrogène.
Lorsque le métal a, malgré les précautions prises, absorbé trop de gaz pour donner des pièces saines, il est possible de le traiter. Différentes méthodes peuvent être employées. La précipitation, qui consiste à faire réagir le gaz dissous avec un élément plus réactif que le métal en fusion, est une des plus courantes. L’élément ajouté, après avoir réagi avec l’oxygène, va former un oxyde qui va flotter à la surface du métal liquide. Cette méthode est très efficace vis-à-vis de l’oxygène : une addition de phosphore désoxyde le cuivre liquide ; le ferromanganèse, le silicium ou l’aluminium sont utilisés pour désoxyder l’acier. On peut également garnir les parois du moule d’un élément ayant ce rôle. Une autre méthode consiste à dégazer le métal en le soumettant au vide : le gaz s’échappe alors comme les bulles s’échappent d’une boisson gazeuse lorsqu’on ouvre la bouteille. Il est également possible de saturer le bain d’un gaz peu soluble (comme l’argon) pour chasser les autres gaz. Ces méthodes pneumatiques sont fréquemment utilisées pour ôter l’hydrogène de l’acier liquide.
La détection des soufflures est difficile. Elles peuvent être confondues avec des cavités produites par d’autres phénomènes (retrait dû à la solidification, etc) lorsqu'elles sont remplies de gaz. Les méthodes de détection utilisées actuellement sont la radiographie, le contrôle par ultrasons et la magnétoscopie.
Défauts dus au matériau du moule
On recense les « collages », …
Défauts dus au remplissage du moule
On recense les « gouttes froides », les « reprises », les « manques » ou « malvenues », …
Défauts métallurgiques
On recense les « criques » qui peuvent être internes ou débouchantes, …
Défauts spécifiques à un procédé de moulage
Défauts de coulée continue
Dans la coulée continue de produits plats (brames), la « crique longitudinale » est une fissure débouchante située au milieu de la grande face de la brame. Elle fait de 5 à 30 mm de profondeur et est longue de plusieurs mètres. Elle est typique d’un refroidissement inadapté en lingotière, et engendre souvent une « percée » de la peau solidifiée, incident de production coûteux et spectaculaire
On rencontre également des « criques transversales », généralement liées à un cintrage ou un décintrage inadapté du produit. Les « gouttières » et le « bombé » sont des déformations longitudinales, respectivement concaves et convexes, typiques d’une mauvaise géométrie de la lingotière. Les « criques internes » sont dues à un mauvais soutien ou guidage du produit dans le refroidissement secondaire : leur position permet d’identifier rapidement l’élément défaillant de la machine.
Au centre du produit, il est fréquent de trouver une « zone de ségrégation », où sont piégés les composés à bas point de fusion. On limite la nocivité de cette zone avec des brasseurs électromagnétiques ou un soutien actif du produit.
Défauts de moulage au sable
Articles connexes
Fonderie
Moulage